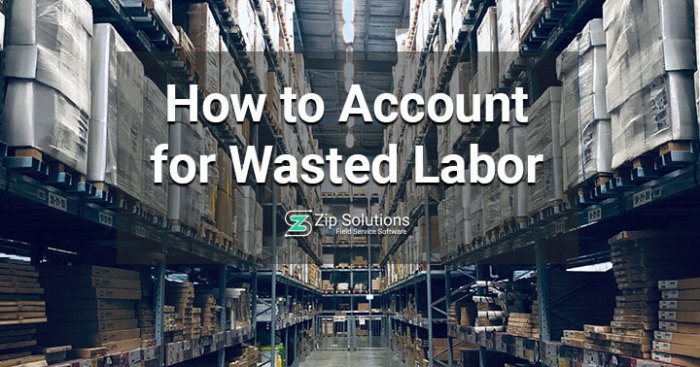
Mathematics of Wasted Labor: An Example
Mathematics of wasted labor an example sets the stage for this enthralling narrative, offering readers a glimpse into a story that is rich in detail and brimming with originality from the outset. Have you ever wondered how much time and resources are wasted in the workplace?
It’s a problem that plagues businesses of all sizes, across all industries. But what if we could quantify this waste, and use that data to make improvements? That’s where the mathematics of wasted labor comes in.
This post will explore the concept of wasted labor, how we can measure it, and the consequences of ignoring it. We’ll also delve into a real-world case study to illustrate how wasted labor can be identified and addressed. By understanding the mathematics of wasted labor, we can take steps to optimize our processes, improve productivity, and ultimately, create a more efficient and effective workplace.
Defining Wasted Labor
Wasted labor, also known as unproductive labor, refers to the time and effort spent on activities that do not contribute to the desired output or value creation. It represents a significant loss for businesses and individuals, as it consumes resources without generating any tangible benefits.
Examples of Wasted Labor
Wasted labor manifests itself in various forms across different industries and professions. Here are some common examples:
- Inefficient Processes:Repetitive tasks, unnecessary paperwork, and cumbersome procedures can lead to wasted labor. For example, a manufacturing company might have a complex approval process for new product designs, resulting in delays and wasted time for engineers.
- Lack of Training:Employees who lack the necessary skills or knowledge to perform their tasks effectively can contribute to wasted labor. For instance, a call center agent who is not properly trained on handling customer complaints might struggle to resolve issues, leading to longer call durations and customer dissatisfaction.
Think about the mathematics of wasted labor in the context of a factory that produces widgets. If they produce 100 widgets, but 20 are defective, that’s 20% wasted effort. The same logic applies to food aid, which can sometimes be seen as a form of “dumping” – food aid as dumping – where surplus agricultural products are shipped to developing countries, potentially undermining local markets and agricultural development.
This not only wastes resources but also undermines the potential for sustainable economic growth in the recipient countries, further highlighting the complex mathematics of wasted labor on a global scale.
- Poor Communication:Miscommunication and lack of clarity in instructions can result in wasted time and effort. For example, if a project team does not have a clear understanding of project requirements, they might spend time working on tasks that are not aligned with the project goals.
- Unnecessary Meetings:Meetings that lack a clear purpose or agenda can be a significant source of wasted labor. For example, a weekly team meeting that simply updates everyone on individual progress might be more efficiently handled through email communication.
Factors Contributing to Wasted Labor
Several factors contribute to wasted labor, including:
- Inefficient Processes:Outdated or poorly designed processes can lead to redundant tasks, bottlenecks, and delays. For example, a company might have a manual process for tracking inventory, which is time-consuming and prone to errors.
- Lack of Automation:Repetitive and manual tasks that could be automated can lead to wasted labor. For example, data entry tasks can be automated using software, freeing up employees to focus on more strategic activities.
- Poor Communication:Miscommunication and lack of clarity in instructions can result in wasted time and effort. For example, if a project team does not have a clear understanding of project requirements, they might spend time working on tasks that are not aligned with the project goals.
Imagine a factory worker spending hours meticulously assembling a product, only to have it deemed defective and scrapped. This is a stark example of wasted labor, a concept deeply intertwined with the principles of a primer on neoliberalism. This ideology, often criticized for prioritizing profit over human well-being, can lead to systems where such inefficiencies are normalized, highlighting the crucial need for a more humane approach to labor and production.
- Lack of Training:Employees who lack the necessary skills or knowledge to perform their tasks effectively can contribute to wasted labor. For instance, a call center agent who is not properly trained on handling customer complaints might struggle to resolve issues, leading to longer call durations and customer dissatisfaction.
Imagine a factory where workers spend hours meticulously assembling products, only to have them rejected due to minor flaws. That’s a perfect example of wasted labor in action. This inefficiency can be found on a larger scale, too, like when trade barriers between countries lead to unnecessary delays and increased costs.
It’s a bit like the complexities of some regional free trade agreements – while they aim to streamline trade, they can also create bureaucratic hurdles that ultimately waste time and resources. Understanding the mathematics of wasted labor, whether it’s on a factory floor or a global scale, is crucial for maximizing efficiency and productivity.
- Lack of Motivation:Employees who are not motivated or engaged in their work might be less productive, leading to wasted labor. For example, an employee who feels undervalued or underutilized might be less likely to put in extra effort.
- Micromanagement:Excessive oversight and control can stifle employee autonomy and creativity, leading to wasted labor. For example, an employee who is constantly being micromanaged might feel less empowered to take initiative and make decisions, resulting in delays and inefficiencies.
The Mathematics of Wasted Labor
Quantifying wasted labor involves applying mathematical concepts to measure the inefficiency in the workforce. This approach helps businesses understand the extent of lost productivity and identify areas for improvement.
Metrics for Measuring Wasted Labor
Various metrics are used to quantify wasted labor, providing insights into different aspects of inefficiency.
- Downtime:This metric measures the time employees are idle due to factors such as equipment failure, material shortages, or waiting for instructions. For instance, if a production line is halted for 30 minutes due to a machine malfunction, this downtime represents wasted labor.
- Rework:This metric quantifies the time and resources spent correcting errors or defects in work already completed. For example, if a team of software developers spends 10 hours fixing bugs in a program, this rework time is considered wasted labor.
- Absenteeism:This metric measures the number of days employees are absent from work due to illness, personal reasons, or other factors. For example, if an employee is absent for 5 days due to illness, this absence contributes to wasted labor.
- Overtime:While overtime might seem like a way to increase productivity, it can also be a sign of inefficiency. If overtime is frequently required to meet deadlines, it suggests that the workload is not adequately managed, resulting in wasted labor.
- Meetings:While meetings are necessary for communication and collaboration, poorly planned or unproductive meetings can waste valuable time. For example, a meeting that lasts an hour but achieves little can be considered wasted labor.
Limitations of Mathematical Measurement
While mathematical concepts provide valuable insights into wasted labor, they have limitations:
It’s important to remember that quantifying wasted labor is just one part of the picture.
- Subjectivity:Some aspects of wasted labor, such as employee motivation or lack of engagement, are difficult to quantify objectively. These factors can significantly impact productivity but are not easily captured by mathematical metrics.
- Contextual Factors:The impact of wasted labor can vary depending on the industry, company size, and specific circumstances. A certain amount of downtime might be acceptable in some industries, while in others, even a few minutes of downtime can be costly.
- Human Element:Mathematical models cannot fully capture the human element of work, such as creativity, innovation, or the impact of teamwork. These factors are crucial for productivity but are not easily measured using quantitative methods.
Case Study: The Healthcare Industry: Mathematics Of Wasted Labor An Example
The healthcare industry, a critical sector in any nation, is often plagued by inefficiencies that lead to wasted labor. This waste can manifest in various forms, from administrative burdens to redundant tasks, ultimately impacting patient care and resource allocation.
Analyzing Wasted Labor in Healthcare, Mathematics of wasted labor an example
This section examines specific examples of wasted labor in the healthcare industry, quantifying the extent of this inefficiency and its potential impact.
Administrative Burden
Administrative tasks consume a significant portion of healthcare professionals’ time, diverting them from direct patient care. This burden includes paperwork, insurance claims processing, and data entry. A study by the American Medical Association found that physicians spend an average of 2 hours per day on administrative tasks, which translates to approximately 500 hours per year.
This wasted time equates to a substantial loss in productivity and potentially delays in patient care.
Redundant Processes
Duplication of effort is another major source of wasted labor in healthcare. This can occur in various areas, such as data entry, patient information retrieval, and scheduling. For instance, multiple healthcare providers may maintain separate patient records, leading to redundant data entry and potential discrepancies.
Inefficient Scheduling
Scheduling inefficiencies can lead to wasted time for both healthcare professionals and patients. For example, patients may have to wait for extended periods due to overbooked schedules or cancellations. This wasted time not only impacts patient satisfaction but also reduces the overall efficiency of the healthcare system.
Lack of Standardization
The lack of standardized procedures and protocols across different healthcare settings can contribute to wasted labor. For instance, different hospitals may use different systems for patient record management, requiring healthcare professionals to learn multiple systems, which can be time-consuming and inefficient.
Limited Use of Technology
The healthcare industry is gradually embracing technology, but there is still room for improvement. For example, telehealth and remote patient monitoring can reduce the need for in-person appointments, but adoption rates vary. By leveraging technology, healthcare providers can streamline processes, reduce administrative burden, and ultimately free up more time for patient care.
Quantifying Wasted Labor
The amount of wasted labor in healthcare is difficult to quantify precisely, but various studies provide estimates. For example, a 2019 report by the Institute of Medicine estimated that administrative complexity in healthcare costs the U.S. economy approximately $265 billion per year.
This includes wasted time and resources associated with administrative tasks, redundant processes, and inefficient scheduling.
Addressing Wasted Labor
Identifying and eliminating wasted labor is crucial for organizations seeking to improve efficiency, boost productivity, and enhance profitability. By understanding the root causes of wasted labor, organizations can implement targeted strategies to optimize their workforce and achieve better outcomes.
Strategies and Solutions for Reducing Wasted Labor
Several strategies can be employed to reduce wasted labor within organizations. These strategies address various aspects of workforce management, aiming to optimize processes and eliminate unnecessary tasks.
- Process Optimization:Streamlining workflows, eliminating redundant steps, and implementing automation tools can significantly reduce wasted labor. This involves analyzing existing processes, identifying bottlenecks, and implementing solutions to improve efficiency. For example, automating repetitive tasks like data entry or scheduling appointments can free up employees’ time for more valuable activities.
- Employee Empowerment:Empowering employees to take ownership of their work and make decisions that directly impact their tasks can reduce wasted labor. This involves providing employees with the necessary training, tools, and resources to perform their jobs effectively and efficiently.
- Performance Management:Implementing robust performance management systems helps identify and address areas where employees are struggling or where processes are inefficient. Regular performance reviews, feedback mechanisms, and training programs can help employees improve their skills and contribute more effectively.
- Technology Adoption:Leveraging technology solutions, such as project management software, collaboration platforms, and communication tools, can streamline workflows and reduce wasted time. These tools can improve communication, collaboration, and task management, ensuring that employees are working efficiently and effectively.
- Flexible Work Arrangements:Implementing flexible work arrangements, such as remote work, flextime, or compressed workweeks, can help reduce wasted labor by allowing employees to manage their work schedules effectively. This can reduce commuting time, improve work-life balance, and enhance employee productivity.
Implementing Solutions for Reducing Wasted Labor
Implementing solutions to address wasted labor requires a structured approach, including clear steps, timelines, and responsible parties.
- Identify and Analyze Wasted Labor:The first step involves identifying areas where wasted labor occurs. This can be achieved through data analysis, employee surveys, and process mapping.
- Develop Solutions:Based on the analysis, develop specific solutions to address the identified areas of wasted labor. These solutions should be tailored to the organization’s specific needs and context.
- Pilot and Evaluate:Implement the solutions on a pilot basis, allowing for testing and refinement before full-scale implementation. This approach helps mitigate risks and ensure the solutions are effective.
- Measure and Track Results:Regularly monitor the impact of the implemented solutions, tracking key performance indicators such as productivity, efficiency, and employee satisfaction.
- Continuous Improvement:Implement a continuous improvement culture, fostering a culture of innovation and seeking ways to further optimize processes and reduce wasted labor.
Benefits and Challenges of Addressing Wasted Labor
Addressing wasted labor offers numerous benefits for organizations, but it also presents challenges that need to be carefully considered.
Benefits
- Increased Productivity:Reducing wasted labor leads to increased productivity, as employees can focus on core tasks and deliver better results.
- Enhanced Efficiency:Streamlining processes and optimizing workflows improve efficiency, resulting in faster turnaround times and reduced costs.
- Improved Employee Morale:Reducing wasted labor can lead to improved employee morale, as employees feel valued and empowered to contribute effectively.
- Cost Savings:By eliminating unnecessary tasks and improving efficiency, organizations can achieve significant cost savings.
- Competitive Advantage:Organizations that effectively address wasted labor can gain a competitive advantage by offering better products or services at lower costs.
Challenges
- Resistance to Change:Employees may resist changes to their work processes, particularly if they are accustomed to doing things a certain way.
- Investment Costs:Implementing solutions to address wasted labor may require significant investment in technology, training, or process changes.
- Data Collection and Analysis:Accurately identifying and measuring wasted labor requires robust data collection and analysis capabilities.
- Time Commitment:Implementing and evaluating solutions requires a significant time commitment from management and employees.
- Maintaining Momentum:Sustaining the momentum of change and ensuring that solutions are implemented consistently can be challenging.