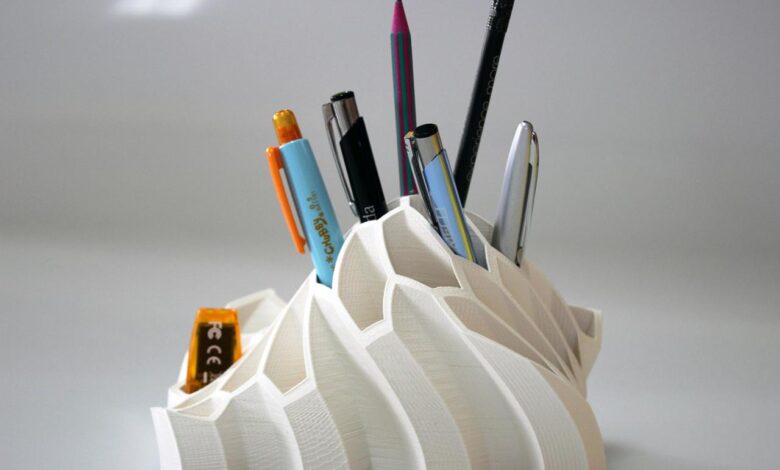
Software Uncovers the 3D Printability of Your Product
Software Uncovers the 3D Printability of Your Product – Imagine transforming your product designs into tangible realities using 3D printing. But before you hit “print,” you need to know if your design is actually printable. That’s where 3D printability analysis software comes in, acting as your guide to a successful 3D printing journey.
This software goes beyond just visualizing your design, it delves into the nitty-gritty details, analyzing your product’s geometry, material properties, and overall complexity to determine if it’s truly ready for the printer.
Think of it as a pre-flight checklist for your 3D print. By analyzing your design, the software highlights potential issues, such as overhangs, thin walls, or unsupported areas, that could cause problems during printing. This early detection saves you time, money, and frustration in the long run.
But it’s not just about identifying problems; 3D printability analysis software also helps you optimize your design for enhanced printability. By suggesting design modifications, the software ensures a smoother printing process, resulting in a higher quality, more robust final product.
The Rise of 3D Printing in Product Design
D printing, also known as additive manufacturing, has revolutionized product design and manufacturing processes across various industries. This technology has emerged as a powerful tool for creating prototypes, producing custom products, and even manufacturing complex designs that were previously impossible to achieve through traditional methods.
Benefits of 3D Printing for Product Development and Prototyping
The adoption of 3D printing has been driven by its numerous benefits, particularly in the early stages of product development and prototyping. 3D printing allows designers and engineers to quickly iterate on designs, experiment with different shapes and materials, and create functional prototypes for testing and validation.
- Rapid Prototyping:3D printing enables rapid prototyping, allowing designers to create physical models of their designs within a short timeframe. This accelerated prototyping process significantly reduces the time and cost associated with traditional methods, such as CNC machining or injection molding.
Imagine a world where software can analyze your product and tell you exactly how to 3D print it, even down to the optimal materials and settings. It’s like having a magic wand that transforms your ideas into tangible objects! This incredible technology can even help you create custom learning experiences for children.
For example, check out 25 five senses activities to engage kids in the world around them , which provides a fun and interactive way to explore the world. Just like this resource, software can help us unlock the potential of 3D printing, making it easier than ever to bring our visions to life.
- Design Flexibility:3D printing offers unparalleled design flexibility, enabling the creation of complex geometries, intricate details, and customized designs that would be difficult or impossible to achieve with conventional methods. This flexibility allows designers to push the boundaries of product design and create innovative solutions.
- Cost-Effectiveness:While 3D printing technology has advanced significantly, it remains a cost-effective solution for prototyping and small-scale production. The ability to print on-demand eliminates the need for large-scale tooling and reduces material waste, making it an attractive option for startups, small businesses, and even large corporations.
- Material Diversity:3D printing technology supports a wide range of materials, including plastics, metals, ceramics, and composites. This material diversity allows designers to select the most suitable material for their specific application, ensuring optimal performance and functionality.
Understanding 3D Printability
D printability refers to the ability of a design to be successfully printed using 3D printing technology. It encompasses a wide range of factors that influence the feasibility and quality of the final printed product. Understanding 3D printability is crucial for designers, as it allows them to create designs that are not only aesthetically pleasing but also manufacturable and functional.
Factors Influencing 3D Printability
The printability of a 3D model depends on various factors, including the chosen material, the geometry of the design, and the complexity of the design.
- Material Properties: Different 3D printing materials possess unique properties that influence their printability. Factors such as the material’s melting point, viscosity, and thermal expansion coefficient play a crucial role in determining the success of the printing process. For instance, materials with high viscosity might be difficult to print in intricate geometries due to their resistance to flow.
Imagine a software that not only designs your product but also analyzes its 3D printability, ensuring a smooth transition from digital model to physical reality. It’s a powerful tool for any innovator, much like the impact Pope Francis is making on the Asia Pacific region with his ambitious tour.
This software can help streamline your production process, just as the Pope’s visit aims to strengthen ties and promote understanding across diverse cultures.
- Geometry: The shape and form of the design significantly impact its printability. Designs with complex geometries, sharp corners, or thin walls can pose challenges for 3D printers. The printer’s nozzle size and the layer thickness influence the resolution and detail achievable in the final print.
- Design Complexity: The complexity of a design, including the number of features, overhangs, and intricate details, can impact its printability. Highly complex designs might require specialized printing techniques or support structures to ensure successful printing.
Design Features Hindering 3D Printability
Certain design features can hinder 3D printability, leading to printing errors, defects, or weak structures.
- Overhangs: Overhangs are features that extend beyond the base of the model without support. These can be difficult to print without support structures, which can later be removed, potentially leaving behind imperfections.
- Thin Walls: Thin walls can be prone to warping or collapsing during the printing process, especially with materials that are prone to shrinkage.
- Sharp Corners: Sharp corners can lead to stress concentrations, potentially causing cracks or breaks in the printed model.
- Undercuts: Undercuts are features that prevent the printer nozzle from accessing certain areas of the model, requiring specialized printing techniques or support structures.
Introducing Software Solutions for 3D Printability Analysis
The rise of 3D printing has brought with it a new set of challenges for designers and engineers. One of the most important challenges is ensuring that a design is printable. This means that the design must be able to be successfully printed by a 3D printer without any issues.
Software solutions for 3D printability analysis are crucial for overcoming these challenges. Software plays a critical role in evaluating 3D printability by analyzing a digital design and identifying potential issues that could arise during the printing process. This analysis helps ensure a successful print and minimizes wasted time, materials, and resources.
Key Functionalities of 3D Printability Analysis Software
Software designed for 3D printability analysis offers a range of functionalities to assess the suitability of a design for 3D printing.
- Geometry Analysis:Software analyzes the geometry of the design to identify potential issues such as sharp corners, thin walls, or unsupported overhangs. These features can cause printing problems, such as breaking, warping, or poor surface finish.
- Material Selection:Software helps select the most appropriate material for the design and printing process based on factors like strength, flexibility, and temperature resistance. This ensures the final product meets the required specifications.
- Support Structure Generation:Software automatically generates support structures for overhangs and complex geometries. These structures provide temporary support during printing, preventing sagging or distortion, and ensuring a clean and accurate print.
- Print Path Optimization:Software optimizes the printing path, ensuring efficient material usage and minimizing printing time. This optimization can significantly impact the cost and efficiency of the printing process.
- Simulation and Visualization:Software simulates the printing process, allowing users to visualize potential problems before printing. This helps identify areas for improvement and reduce the risk of printing failures.
Comparison of 3D Printability Analysis Software Solutions
Several software solutions are available for 3D printability assessment, each offering unique features and capabilities.
- Meshmixer:This free and open-source software offers basic printability analysis features like geometry inspection and support structure generation. It is suitable for simple designs and personal projects.
- Netfabb:A commercial software with advanced printability analysis capabilities, including detailed geometry analysis, support structure optimization, and print path optimization. It is suitable for professional users and industrial applications.
- Simplify3D:This software offers a user-friendly interface and integrates with various 3D printers. It provides basic printability analysis features, including geometry inspection and support structure generation. It is suitable for both hobbyists and professionals.
- Ultimaker Cura:This free and open-source software is specifically designed for Ultimaker 3D printers. It offers basic printability analysis features, including geometry inspection and support structure generation. It is suitable for users of Ultimaker 3D printers.
Analyzing Product Designs for 3D Printability: Software Uncovers The 3d Printability Of Your Product
Once you have a 3D model of your product, the next step is to analyze its 3D printability. This involves assessing whether the design can be successfully printed using a 3D printer and identifying potential issues that may arise during the printing process.
Software-Based Analysis, Software uncovers the 3d printability of your product
Analyzing a product’s 3D printability using software involves a series of steps that help identify potential issues and ensure a successful print.
It’s amazing how software can now analyze a product design and determine its 3D printability. This technology is a game-changer for manufacturers, allowing them to quickly assess feasibility and optimize designs for production. Speaking of game-changers, the upcoming fight between Dan Azeez and Lewis Edmondson, added to the Adam Azim vs.
Ohara Davies undercard, is sure to be a thrilling event. Just like 3D printing software helps streamline production, this fight promises to bring excitement and action to the boxing world. So, keep an eye out for both the advancements in 3D printing technology and the exciting boxing match coming soon!
- Import the 3D Model:Begin by importing the 3D model of your product into the chosen software. The software should support common file formats like STL, OBJ, or IGES.
- Analyze Geometry:The software will analyze the model’s geometry to identify any potential issues related to 3D printing. This includes:
- Overhanging Features:Features that extend beyond the support structure and could potentially sag or deform during printing.
- Thin Walls:Walls that are too thin might not have enough material to maintain their shape during printing.
- Sharp Corners and Edges:Sharp corners and edges can be difficult to print cleanly and may require additional support structures.
- Unsupported Features:Features that lack sufficient support from the print bed or surrounding geometry and might detach during printing.
- Internal Cavities:The presence of internal cavities can complicate printing and may require special techniques to ensure proper filling.
- Identify Support Structures:The software can automatically generate support structures for overhanging features or complex geometries. It’s crucial to analyze the generated support structures to ensure they are adequately positioned and won’t interfere with the final product.
- Assess Material Compatibility:Different materials have varying properties and limitations. The software can help determine the suitability of the chosen material for the design. Factors like the material’s strength, flexibility, and thermal properties need to be considered.
- Analyze Print Orientation:The software can simulate different print orientations to identify the optimal position for printing. This involves considering factors like support structure requirements, print time, and potential for warping or deformation.
- Estimate Print Time and Cost:Based on the model’s complexity, material selection, and print orientation, the software can provide estimates for the print time and cost. This helps in planning and budgeting for the 3D printing process.
Step-by-Step Guide for 3D Printability Analysis
Let’s illustrate the analysis process using a specific software tool, ” [Software Name]“. This software offers a comprehensive suite of features for analyzing 3D printability.
- Install and Launch the Software:Download and install [Software Name]on your computer. Launch the software and create a new project.
- Import the 3D Model:Click on ” Import” and select the 3D model file (e.g.,.stl) from your computer. The model will appear in the software’s 3D workspace.
- Analyze Geometry:Navigate to the ” Analysis” tab and select ” Geometry Analysis“. The software will automatically scan the model for potential issues like overhangs, thin walls, and sharp corners. The results will be displayed in the ” Issues” panel.
- Generate Support Structures:Click on ” Support Structures” and select the desired support structure type. The software will automatically generate support structures based on the model’s geometry and the chosen settings.
- Evaluate Support Structures:Carefully examine the generated support structures to ensure they are adequately positioned and won’t interfere with the final product. You can adjust the support structure settings if needed.
- Choose Material:Go to the ” Materials” tab and select the desired material from the list. The software will display the material properties and limitations.
- Analyze Print Orientation:Select the ” Orientation” tab and experiment with different print orientations. The software will display the support structure requirements and potential for warping or deformation for each orientation.
- Estimate Print Time and Cost:Based on the chosen material, print orientation, and other settings, the software will provide estimates for the print time and cost. This information will help you plan your printing process and budget.
Interpreting Analysis Results
The software’s analysis results will highlight potential issues related to 3D printability. It’s essential to understand how to interpret these results and take appropriate action.
- Overhangs:The software will identify areas with overhangs that exceed a specific angle threshold. You can either adjust the model to reduce the overhang angle or add support structures to prevent sagging or deformation.
- Thin Walls:The software will flag walls that are thinner than a specific threshold. You can thicken the walls in the model or consider using a different material with better strength properties.
- Sharp Corners and Edges:The software will highlight sharp corners and edges that might be difficult to print cleanly. You can round off these features in the model or use a higher resolution print setting to improve the print quality.
- Unsupported Features:The software will identify features that lack sufficient support and could detach during printing. You can add support structures or modify the model to provide adequate support.
- Internal Cavities:The software will indicate the presence of internal cavities. You can consider using a material that can be easily filled or explore alternative printing techniques to handle these cavities.
- Material Compatibility:The software will assess the chosen material’s suitability for the design based on its properties and limitations. If the chosen material is not compatible, you may need to explore alternative materials.
- Print Orientation:The software will recommend the optimal print orientation based on support structure requirements, print time, and potential for warping or deformation. You can choose the orientation that minimizes support structure requirements and maximizes print quality.
- Print Time and Cost:The software’s estimates for print time and cost will help you plan your printing process and budget. You can adjust the settings or consider alternative materials to optimize print time and cost.
Optimizing Designs for Enhanced 3D Printability
The journey from digital design to a physical 3D printed object is significantly impacted by the design’s printability. Software tools play a crucial role in optimizing product designs to ensure successful 3D printing. These tools analyze designs for potential issues, suggest improvements, and ultimately help create prints that are strong, detailed, and efficient to produce.
Design Modifications for Enhanced 3D Printability
Software tools offer a range of features that facilitate design modifications to improve 3D printability. By analyzing the design, these tools identify areas that might lead to printing difficulties and suggest solutions.
- Support Structures:Overhanging features in a design require support structures to prevent sagging during printing. Software can automatically generate these supports, ensuring they are strategically placed and minimize material waste.
- Wall Thickness:Thin walls can be prone to warping or collapsing during printing. Software tools can analyze wall thickness and suggest adjustments to ensure adequate structural integrity.
- Draft Angles:Draft angles are slight tapers added to vertical surfaces to facilitate easy removal from the print bed. Software can automatically add these angles to prevent parts from sticking and ensure clean detachment.
- Fillet Radii:Sharp corners can cause stress points and printing difficulties. Software tools can round off corners with fillet radii, improving the overall strength and aesthetic appeal of the printed object.
Impact of Design Optimization on Printed Products
Optimizing designs for 3D printability yields several benefits in the final printed product.
- Reduced Printing Time:By minimizing the need for extensive support structures and ensuring optimal print parameters, design optimization can significantly reduce the time required for printing.
- Improved Surface Finish:Optimized designs with appropriate draft angles and rounded corners result in smoother surfaces with fewer imperfections, enhancing the overall aesthetic appeal of the printed object.
- Enhanced Strength:By adjusting wall thickness and incorporating fillet radii, design optimization ensures structural integrity and improves the overall strength and durability of the printed product.
Case Studies
The real-world applications of 3D printability analysis software demonstrate its significant impact on product design and manufacturing. These case studies highlight how the software addresses specific challenges and optimizes the product development process.
Case Study: Automotive Industry
This case study explores how 3D printability analysis software helped an automotive manufacturer optimize the design of a complex car part. The manufacturer faced challenges related to the part’s intricate geometry and the need for high-strength material.
- The software analyzed the part’s design and identified areas prone to failure during 3D printing.
- It suggested design modifications to improve printability and enhance the part’s strength.
- The manufacturer implemented these modifications, resulting in a successful 3D-printed part that met all performance requirements.
The software’s analysis helped the manufacturer overcome the challenges of complex geometry and material selection, ultimately leading to a successful and efficient production process.
Case Study: Medical Devices
This case study examines the role of 3D printability analysis software in the development of a customized medical implant. The manufacturer needed to ensure the implant’s intricate design and biocompatibility for safe and effective use.
- The software simulated the 3D printing process, identifying potential issues related to overhangs and support structures.
- It suggested design adjustments to optimize the implant’s printability and maintain its biocompatibility.
- The software also analyzed the implant’s mechanical properties, ensuring its strength and durability.
The software’s comprehensive analysis helped the manufacturer develop a highly customized medical implant that met stringent safety and performance standards.
Case Study: Aerospace Industry
This case study explores how 3D printability analysis software helped an aerospace company design a lightweight and durable aircraft component. The company faced challenges related to the component’s complex geometry and the need for high-strength material.
- The software analyzed the component’s design, identifying areas prone to stress concentration and failure.
- It suggested design modifications to optimize the component’s weight and strength while maintaining its structural integrity.
- The software also simulated the 3D printing process, ensuring the component’s printability and minimizing material waste.
The software’s analysis enabled the aerospace company to develop a lightweight and durable aircraft component that met all performance requirements.
Case Study: Consumer Products
This case study demonstrates how 3D printability analysis software helped a consumer product manufacturer design a functional and aesthetically pleasing product. The manufacturer faced challenges related to the product’s complex geometry and the need for a visually appealing finish.
- The software analyzed the product’s design, identifying potential issues related to overhangs and support structures.
- It suggested design modifications to optimize the product’s printability and enhance its visual appeal.
- The software also analyzed the product’s surface finish, ensuring its smoothness and aesthetic quality.
The software’s analysis enabled the manufacturer to develop a functional and aesthetically pleasing product that met customer expectations.